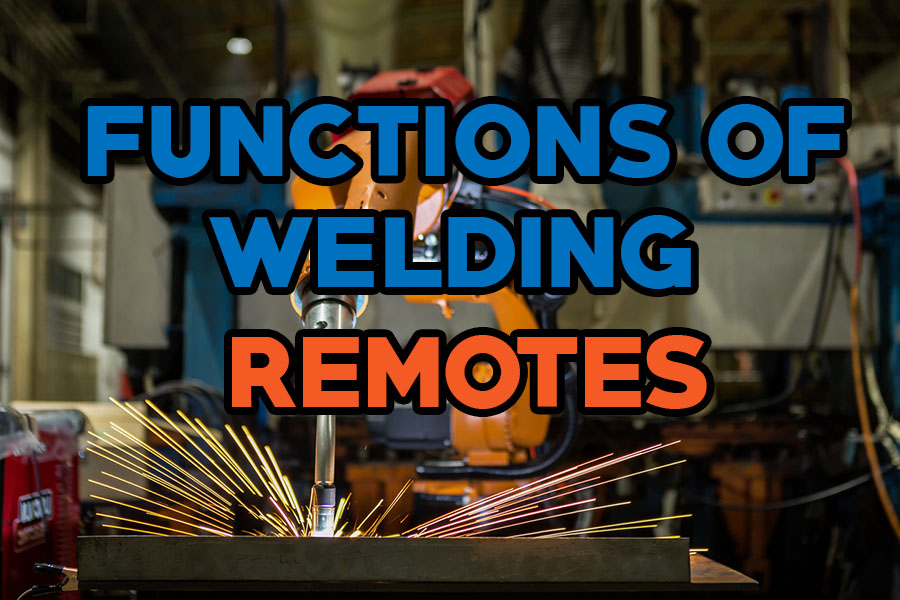
In welding, it’s not the welding itself that’s the hardest. When you are welding under the wing structure of an airplane, or hanging from rafters two stories above a shop floor, there is no place like the engine compartment of a car to do it. A common aspect of welding is uncomfortable, awkward, or inaccessible positions. This is why you should consider getting a welding remote control. Operators can work in dangerous places with these remote controls.
The Goal of Welding
In general, welding makes a firm connection between two elements. Binding metals or thermoplastics together is a common practice among welders. Skyscrapers, cars, ships, and airplanes are all constructed using welding in our world today.
Previously, builders joined metal workpieces using other methods. Welding can be replaced with soldering, brazing, or riveting. Why welding is such a highly prized skill in industrial applications and manufacturing, and why it has become the standard joining option for many industries.
Welding remotes: What functions do they provide?
Several of the functions found on different welding power supplies can be replicated by orbital remote welding control units. There are a couple of controls that allow you to adjust welding heat and weld head motion as well as control some of the purging gas.
There are a number of keys on welding control units, including those below:
All stop key: This key initiates a post-weld purge of the system after all parts of the welding operation are stopped.
Rotation jog CW key: In this case, the electrode will be rotated clockwise by the orbital weld head.
Rotation jog CCW key: As a result, the electrode of the orbital welding head is rotated counterclockwise.
Sequence start key: Welding is initiated by pressing the sequence start key according to the welding parameters loaded.
Sequence stop key: When the welding machine receives this instruction, it stops working. Even after welding is restarted, the shielding gas remains on.
Amps up key: By pressing this key, a higher current frequency will be supplied by the welding power supply, resulting in an increase in arc temperature.
Amps down key: In addition to reducing the heat generated by the welding arc, this key also reduces the amperage of the welding power supply current.
Manual purge key: When the button is pressed, the gas solenoid activates, and remains active until it is deactivated.
Weld number key: Using the preset list of weld parameters, the welder can choose what parameters to use.
Weld/test mode key: The welder can observe the orbital welder’s movements and ensure the welding parameters have been set correctly by this method, which initiates the orbital welder through the motions set by the welding parameters without initiating an arc.
A Remote Welding Control Unit: When Is It Needed?
In addition to allowing welding settings to be adjusted midway through welding, remote welding control units also help reduce time spent returning to the welding power supply. The remote welding control unit controls manual welders in this manner. If the weld runs too hot, too cold, or too slowly, the weld operator can adjust the machine when observing the results.
Faqs
Question 1: Why do welders use a remote control?
Answer: As welding parameters are set at joints using remote control technology, welding operators have become increasingly dependent on it. As a result, safety can be improved and production can be increased because fewer trips are needed to and from the power source.
Question 2: How does a remote control system benefit you?
Answer: It enables you to operate any machine or device wherever you are, no matter what the circumstances may be. As a result, you can do a lot of tasks in less time.